图书介绍
盛世新管理书架 Lean TPM精益设备 事后维修与综合效率提升你也可以懂!PDF|Epub|txt|kindle电子书版本网盘下载
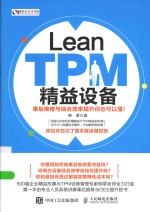
- 柳草著 著
- 出版社: 北京:人民邮电出版社
- ISBN:9787115401168
- 出版时间:2015
- 标注页数:359页
- 文件大小:47MB
- 文件页数:376页
- 主题词:企业管理-生产管理
PDF下载
下载说明
盛世新管理书架 Lean TPM精益设备 事后维修与综合效率提升你也可以懂!PDF格式电子书版下载
下载的文件为RAR压缩包。需要使用解压软件进行解压得到PDF格式图书。建议使用BT下载工具Free Download Manager进行下载,简称FDM(免费,没有广告,支持多平台)。本站资源全部打包为BT种子。所以需要使用专业的BT下载软件进行下载。如BitComet qBittorrent uTorrent等BT下载工具。迅雷目前由于本站不是热门资源。不推荐使用!后期资源热门了。安装了迅雷也可以迅雷进行下载!
(文件页数 要大于 标注页数,上中下等多册电子书除外)
注意:本站所有压缩包均有解压码: 点击下载压缩包解压工具
图书目录
第Ⅰ部分 精益事后维修管理3
第1章 故障的基本概念3
1.1何谓设备故障4
1.2故障的种类及其区分6
第2章 设备突发故障(异常)作业流程13
2.1设备故障的具体征兆16
2.2维修人员去向管理17
2.3异常发生前作业记录19
2.4查看事故事实材料记录技巧20
2.5维修前进行必要的现场调查以了解有关事实20
2.6快速故障分析与排查21
2.6.1两种故障分析的进行方式21
2.6.2简易故障分析5种工具23
2.6.3创新故障分析的3个手段33
2.7故障原因的分类40
2.7.1故障现象的管理性分类40
2.7.2故障现象的技术性分类45
2.8故障处理的思路方法47
2.8.1通过故障曲线了解排除故障47
2.8.2故障处理的通用步骤49
2.8.3维修人员的“问望听闻切拽”六字诀50
2.8.4设备故障排除七字经56
2.8.5电气故障排除的10个原则56
2.8.6快速故障检查与排除的KNOW-HOW58
2.8.7日企设备故障五大成因对策60
2.8.8从事后维修到主动维修64
2.9故障维修时间缩短的5种对策65
2.9.1有图纸设备故障的快速维修65
2.9.2无图纸电气设备的快速维修66
2.9.3维修业也需要快速专家会诊67
2.9.4快速维修亦需零件安装标准化67
2.9.5结合实际选择赛车式快速维修71
2.10维修作业现场安全管理72
2.10.1行为管理的手指口述73
2.10.2维修人员的劳保工具管理76
2.10.3设备维修的上锁挂牌管理78
2.10.4发生事故后怎么办83
2.11做好维修验收的途径85
2.11.1通过产品检验维修质量85
2.11.2采用标准评判维修质量87
2.11.3通过冷态和热态进行验收93
2.11.4构建体系管控维修质量95
2.12维修现场的3S管理98
2.13切实做好维修过程记录102
2.13.1规范填写维修记录102
2.13.2填写维修记录不得不知的专业术语104
2.13.3维修记录填写问题的规避107
2.14设备停机异常上报流程108
2.15机台设备“病历卡”管理115
2.16务必做好故障统计120
2.17长时间故障管理124
2.18重要故障分析管理124
2.19故障再发防止对策126
2.19.1纠正与预防的异同126
2.19.2再发防止定义127
2.19.3再发防止的目的128
2.19.4再发防止的步骤128
2.19.5再发防止追求的结果129
2.19.6注意开好再发防止对策会议129
2.19.7再发、多发故障防止对策130
2.19.8防止设备故障发生的技术性措施130
2.19.9如何避免老问题重复发生132
2.20故障对应时间推移管理134
第3章 故障维修管理的两个方向135
3.1通过作业要领书修好故障136
3.1.1作业要领书的分类137
3.1.2作业要领书包含的六项内容137
3.1.3作业要领书的编制要点138
3.2找对思路防止故障再发142
第4章 避免设备故障的4个方面143
4.1夯实维修基础管理144
4.1.1目视化看板145
4.1.2日常行为管理145
4.1.3技术管理147
4.2打造预防为主机制147
4.2.1预防维修148
4.2.2改良保全148
4.3营造全员参与氛围148
4.4举一反三他机点检150
4.4.1他机点检的概念151
4.4.2他机点检活动开展流程151
4.4.3他机点检案例:马自达电动车驱动系统故障154
第5章 精益事后维修管理常用表单157
5.1设备病历卡1158
5.2设备病历卡2159
5.3设备维修通达及记录书160
5.4设备维修记录表161
5.5机床故障分析报告162
5.6班设备故障停机记录表163
5.7设备故障停机时间推移图164
5.8故障对应时间次数推移165
5.9 ××车间故障统计分析总表166
5.10 Why-Why问题分析表167
5.11 ××设备故障字典168
5.12设备操作指导书169
5.13维修人员劳保用品的标准配置表170
5.14维修工作业伤害预警防范应急措施171
5.15维修技术标准172
5.16长时间故障维修记录173
5.17重大停故障报告书174
5.18重大故障报告书175
5.19年度重大停故障管理表176
5.20年度重复故障管理表177
5.21维修月度报告书(××××年×月)178
5.22维修作业要领书179
5.23专业维修作业要领书180
5.24再、多发故障防止对策表181
第Ⅱ部分 设备综合效率提升185
第6章 设备综合效率管理基础185
6.1何谓设备综合效率188
6.1.1设备综合效率概念解读188
6.1.2设备综合效率基本公式189
6.2实行OEE的作用190
6.3通过OEE管理改良企业业绩191
6.4 OEE与设备损失的关系192
6.4.1设备六大损失192
6.4.2设备八大损失196
6.5设备综合效率计算198
6.5.1时间开动率198
6.5.2性能开动率198
6.5.3合格品率203
6.5.4 OEE的计算案例203
6.5.5 OEE的应用范围207
6.6回归OEE的最本质对标意义208
6.7使用OEE时的困惑与注意事项212
6.7.1使用OEE时的困惑和误区212
6.7.2使用OEE时的注意事项212
6.8 OEE数据采集记录212
6.8.1 OEE数据采集常用的方式212
6.8.2如何保证数据采集的准确性215
第7章 设备六大损失分析与对策219
7.1 OEE提升小组应关注的问题220
7.2故障停机损失的出路221
7.2.1企业故障次数居高不下的原因221
7.2.2简单有效的故障分析工具223
7.2.3 PM慢性故障解析法225
7.2.4从维护总成本角度来看零故障管理三步骤232
7.2.5建立故障对策信息库,维修时间缩短235
7.2.6零故障实施的三大方向236
7.3 SMED产品切换损失的法宝240
7.3.1快速切换的基本常识240
7.3.2 SMED常见概念理解242
7.3.3快速切换的步骤243
7.3.4注意总结快速切换的方法与要点246
7.3.5快速换模的七大法则248
7.3.6开好快速切换现场分析会256
7.3.7快速切换效果看得见256
7.4小停机短暂停机损失管理257
7.4.1小停机基本概念257
7.4.2短暂停机的特征257
7.4.3短暂停机的结果258
7.4.4故障停机与短暂停机的差异258
7.4.5小停机瞬间停止损失分析思路259
7.4.6小停机改进16步骤260
7.4.7短暂停机的现象与原因举例262
7.4.8短暂停机改善着手点263
7.4.9短暂停机改善系统案例264
7.5速度损失分析管理272
7.5.1速度损失分析的七个步骤(图7-13)272
7.5.2提升设备速度改善思路273
7.6废品及返工分析274
7.6.1废品及返工分析对应OEE质量损失274
7.6.2作业失误后果与原因对策分析(图7-15)275
7.6.3废品返工对策的7个步骤(表7-57)275
7.6.4通过故障树差分析品质不良的原因276
7.6.5减少返工损失改善个案(表7-59)277
7.6.6通过防呆纠错技术减少质量损失278
7.6.7透过主动检测减少废料损失案例(图7-16)279
7.6.8通过管理提升促进质量改善283
7.7透过简单、标准的检查程序来减少启动损失287
7.8某企业OEE六大LOSS降低的基本对策(表7-69)289
7.9改善要素总结289
第8章 OEE提升管理推进291
8.1 OEE指标分解292
8.2常用工具方法介绍294
8.3 OEE效率提升的十步骤(表8-5)298
8.4抓好OEE改善过程中的小组分析会议管理299
8.4.1与操作员在车间以小时进行沟通300
8.4.2下班前的业绩对话301
8.4.3周问题排查会议302
8.4.4与运营经理的业绩对话304
8.5 OEE的跟踪305
8.5.1确定跟踪时间、跟踪数量305
8.5.2计划与实际的比对307
8.5.3确定计算OEE的速度307
8.6通过小组活动实现业绩提升308
8.7企业其他效率提升空间309
8.8改善管理应注意的四个方面311
8.8.1改善活动必须要有很明确的目的311
8.8.2必须要触及根本原因(Root cause)311
8.8.3必须要标准化313
8.8.4一定要善用激励313
第9章 OEE体系构建与信息化建设315
9.1构建OEE体系的八步骤316
9.2 OEE管理实施过程中的常见问题318
9.3设备故障管理系统321
9.3.1故障异常综合平台322
9.3.2故障体系平台324
9.3.3故障分析云平台331
9.3.4移动故障管理平台335
9.3.5 Andon报修平台338
9.4企业OEE管理办法案例340
9.5××汽车厂OEE管理办法案例342
第10章 设备综合效率提升常用表单347
10.1设备OEE停机记录表348
10.2设备每日运行记录表349
10.3每日停机记录350
10.4 OEE每周数据汇总表351
10.5设备效率计算表352
10.6潜在失效模式和后果分析(过程FMEA)353
10.7快速切换(SMED)改善用纸354
10.8 SMED快速切换指导书355
10.9 SMED快速切换查核表356
后记357
参考文献359