图书介绍
大中型光学非球面镜制造与测量新技术PDF|Epub|txt|kindle电子书版本网盘下载
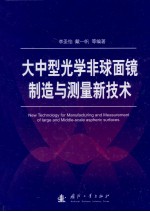
- 李圣怡等编著 著
- 出版社: 北京:国防工业出版社
- ISBN:9787118072372
- 出版时间:2011
- 标注页数:628页
- 文件大小:187MB
- 文件页数:673页
- 主题词:非球面透镜-制造-技术;非球面透镜-测量技术
PDF下载
下载说明
大中型光学非球面镜制造与测量新技术PDF格式电子书版下载
下载的文件为RAR压缩包。需要使用解压软件进行解压得到PDF格式图书。建议使用BT下载工具Free Download Manager进行下载,简称FDM(免费,没有广告,支持多平台)。本站资源全部打包为BT种子。所以需要使用专业的BT下载软件进行下载。如BitComet qBittorrent uTorrent等BT下载工具。迅雷目前由于本站不是热门资源。不推荐使用!后期资源热门了。安装了迅雷也可以迅雷进行下载!
(文件页数 要大于 标注页数,上中下等多册电子书除外)
注意:本站所有压缩包均有解压码: 点击下载压缩包解压工具
图书目录
上篇 制造技术2
第一章 现代非球面光学研抛技术基础2
1.1 光学非球面的优点及应用2
1.1.1 光学非球面的优点2
1.1.2 非球面光学零件在军用装备的应用3
1.1.3 非球面光学零件在民用装备的应用4
1.2 光学非球镜制造的特点5
1.2.1 现代光学系统对非球面光学零件的要求5
1.2.2 非球面光学零件的加工分析9
1.3 超光滑表面制造技术12
1.3.1 超光滑表面及应用12
1.3.2 超光滑表面制造技术概述15
1.3.3 基于机械微切削原理的超光滑表面制造技术16
1.3.4 传统游离磨料抛光的超光滑表面制造技术17
1.3.5 非接触超光滑抛光原理和方法20
1.3.6 非接触化学机械抛光方法(CMP)22
1.3.7 磁场效应辅助加工技术23
1.3.8 粒子流加工技术23
1.4 先进非球面光学研抛技术25
1.4.1 非球面光学零件的经典研抛方法25
1.4.2 非球面光学零件的现代数控研抛方法26
1.4.3 非球面光学零件的可控柔体研抛技术27
参考文献34
第二章 非球面光学研抛技术的基础理论37
2.1 光学机械研抛技术的Preston方程及其应用37
2.2 非球面加工的确定性成形原理40
2.3 非球面加工的成形过程理论分析42
2.3.1 非球面加工的成形过程双级数模型42
2.3.2 去除函数尺寸大小对加工的影响43
2.3.3 去除函数扰动影响45
2.3.4 定位误差影响48
2.3.5 离散间隔影响49
2.4 全口径线性扫描方式面形修正理论51
2.4.1 基于Bayesian的迭代算法52
2.4.2 脉冲迭代方法59
2.4.3 截断奇异值分解法60
2.5 极轴扫描方式面形修正技术62
2.5.1 去除函数具有(近似)回转对称特性62
2.5.2 去除函数不具有回转对称特性65
2.6 成形的频域分析68
2.6.1 一般成形条件下的频谱特征69
2.6.2 回转对称型去除函数的修形能力70
2.7 熵最大研抛原理71
2.7.1 研抛熵原理表述72
2.7.2 最大熵原理在定偏心平面研抛中应用的实例74
2.7.3 基于最大熵原理的双转子小工具加工工艺参数的选择的实例77
2.7.4 基于熵增原理抑制磁流变修形中、高频误差的实例78
参考文献83
附录A 两维Hermite级数85
附录B 两维Fouier级数87
附录C 驻留时间双级数模型求解88
附录D 驻留时间双级数模型求解误差分析90
第三章 基于小研抛盘工具的CCOS技术92
3.1 基于小研抛盘工具的CCOS技术综述92
3.1.1 小工具CCOS技术进展92
3.1.2 研抛盘小工具CCOS技术的关键问题94
3.2 AOCMT光学非球面加工机床96
3.3 去除函数的建模与分析98
3.3.1 理想去除函数的特性98
3.3.2 理论模型99
3.3.3 实验模型100
3.3.4 去除函数的修形能力分析102
3.3.5 复杂形状研抛盘去除函数的建模和特性分析105
3.4 CCOS技术中驻留时间算法及分析110
3.4.1 基于加工时间的脉冲迭代法110
3.4.2 卷积效应对残留误差的影响112
3.5 边缘效应下的去除函数建模118
3.5.1 抛光模露边时的压力分布119
3.5.2 边缘效应下的去除函数建模121
3.6 光学表面小尺度制造误差的产生原因与修正方法126
3.6.1 光学表面小尺度制造误差的产生原因与评价方法126
3.6.2 小尺度制造误差的全口径均匀抛光修正法128
3.6.3 小尺度制造误差的确定区域修正法137
3.7 大中型非球面研抛加工控制策略及实验140
3.7.1 大中型非球面的制造工艺路线和研抛加工控制策略140
3.7.2 φ500mm抛物面镜加工实验142
参考文献145
第四章 离子束抛光技术148
4.1 离子束抛光技术概述148
4.1.1 离子束加工技术应用148
4.1.2 光学镜面离子束抛光的基本原理与特点150
4.1.3 光学镜面离子束抛光技术的发展153
4.2 光学镜面离子束抛光的基本理论156
4.2.1 离子溅射过程描述156
4.2.2 离子束抛光材料去除率159
4.3 离子束抛光去除函数建模分析167
4.3.1 离子束抛光去除函数理论建模167
4.3.2 离子束抛光去除函模型特性分析172
4.3.3 离子束抛光去除函模型试验建模177
4.4 离子束加工系统设计与分析180
4.4.1 系统构建180
4.4.2 系统分析181
4.5 离子束抛光面形误差收敛与精度预测预报188
4.6 离子束抛光的小尺度误差演变192
4.6.1 表面粗糙度演变192
4.6.2 微观形貌演变194
4.7 离子束抛光试验199
4.7.1 平面光学镜面抛光试验199
4.7.2 曲面修形试验203
参考文献205
第五章 磁流变抛光技术208
5.1 磁流变抛光技术概述208
5.1.1 磁流体的应用208
5.1.2 光学零件磁场效应辅助抛光技术的发展状况210
5.1.3 确定性磁流变抛光技术发展状况211
5.2 磁流变抛光材料去除机理与数学模型216
5.2.1 磁流变抛光的材料去除机理216
5.2.2 单颗磨粒所受载荷与压入深度理论计算219
5.2.3 磁流变抛光区域流体动力学分析与计算221
5.3 磁流变抛光机床229
5.3.1 磁流变抛光机床结构的基本要求229
5.3.2 磁流变抛光实验样机的机床结构232
5.3.3 倒置式磁流变抛光装置的设计233
5.3.4 磁流变液的循环控制系统236
5.4 磁流变抛光液及其性能测试研究240
5.4.1 磁流变抛光液研制的发展现状240
5.4.2 磁流液的组成成分及性能评价241
5.4.3 磁流变液的组成选择原则246
5.4.4 磁流变抛光液配制实例249
5.4.5 磁流变抛光液的性能测试研究250
5.5 磁流变抛光工艺参数优化256
5.5.1 磁流变抛光工艺参数正交实验256
5.5.2 灰色关联分析258
5.5.3 多项工艺指标的参数优化261
5.5.4 加工过程综合优化262
5.6 磁流变抛光的光学表面成形技术及加工实例263
5.6.1 MRF的计算机控制光学表面成形(CCOS)技术263
5.6.2 光学零件磁流变成形抛光驻留时间求解基本算法264
5.6.3 光学零件磁流变成形抛光实例267
5.7 磁射流抛光技术研究277
5.7.1 磨料射流抛光技术概述277
5.7.2 磁射流聚束稳定性分析280
5.7.3 磁射流抛光去除机理的CFD分析284
5.7.4 光学零件磁射流修形抛光实验287
参考文献290
第六章 确定性光学加工误差的评价方法293
6.1 概述293
6.2 常用的光学加工误差评价方法294
6.2.1 光学加工误差的几何精度评价参数295
6.2.2 基于功率谱密度特征曲线的光学加工误差评价296
6.2.3 基于散射理论的光学加工误差评价297
6.2.4 基于统计光学理论的光学加工误差评价298
6.3 光学加工误差分布特征的分析方法299
6.3.1 光学表面任意方向加工误差的评价与分析299
6.3.2 光学表面局部误差的评价与分析305
6.3.3 工艺方法对光学加工误差的影响分析307
6.4 光学加工误差的散射性能评价方法321
6.4.1 光学加工误差的二进频带划分方法321
6.4.2 基于Harvey-Shack散射理论的误差评价方法325
6.4.3 光学加工误差对散射性能的影响分析326
6.5 基于光学性能分析的频带误差评价方法330
6.5.1 不同频带误差对光学性能的影响特点330
6.5.2 光学系统应用场合对频带误差的要求333
6.5.3 φ200mm抛物面镜离子束加工误差的评价339
参考文献343
下篇 测量技术346
第一章 大中型光学镜面制造中的测量技术346
1.1 绪论346
1.1.1 大中型光学镜面的需求概述346
1.1.2 大中型光学镜面制造中的测量概况350
1.2 大中型光学镜面制造中的坐标测量技术原理351
1.3 大中型光学镜面制造中的干涉零位测量技术352
1.3.1 干涉零位测量技术基本原理352
1.3.2 大中型平面和球面的零位测试技术354
1.3.3 二次非球面曲面的无像差点法零位测试技术356
1.3.4 非球面镜的补偿检验技术359
1.3.5 计算机生成全息图测试技术361
1.4 大中型光学镜面制造中的非零位测量技术368
1.4.1 剪切干涉测量369
1.4.2 高分辨率CCD方法370
1.4.3 欠采样干涉测量方法370
1.4.4 长波干涉测量方法371
1.4.5 双波长干涉测量方法372
1.4.6 子孔径拼接干涉测量方法372
1.5 相位恢复技术373
1.6 亚表面质量检测技术373
1.7 大中型光学镜面制造中的测量实例374
1.7.1 中国2.16m天文望远镜测量实例374
1.7.2 GMT望远镜测量实例375
1.7.3 JWST望远镜测量实例379
1.7.4 GTC望远镜测量实例381
1.7.5 MMT望远镜次镜测量实例384
1.7.6 SPICA望远镜测量实例385
1.7.7 QED Technologies公司子孔径拼接干涉测量386
1.7.8 大型平面镜制造中的在位检测388
参考文献390
第二章 光学非球面坐标测量技术393
2.1 光学非球面坐标测量技术的研究现状与发展趋势393
2.1.1 光学非球面坐标测量技术的地位和特点393
2.1.2 光学非球面坐标检测国内外研究现状与发展趋势394
2.2 大口径非球面直角坐标测量技术研究403
2.2.1 直角坐标测量系统的设计403
2.2.2 大型非球面镜直角坐标测量原理410
2.2.3 基于多截线测量的光学非球面面形误差分析与评定412
2.2.4 加工检测实例——φ500mm非球面镜的加工与检测423
2.3 大型非球面摆臂式测量技术研究426
2.3.1 测量原理分析426
2.3.2 测量系统结构设计430
2.3.3 测量系统精度分析与建模432
2.3.4 摆臂式轮廓法测量非球面顶点曲率半径优化算法438
2.3.5 测量算法仿真与测量试验441
2.4 基于多段拼接的高陡度非球面坐标检测理论与算法444
2.4.1 测量原理与数学模型444
2.4.2 基于最小二乘的迭代算法447
2.4.3 分段轮廓的自动划分与算法仿真449
2.4.4 测量试验451
参考文献453
第三章 子孔径拼接测量方法457
3.1 概述457
3.1.1 子孔径拼接测量的基本原理457
3.1.2 子孔径拼接测量的发展概况457
3.2 子孔径拼接基本算法461
3.2.1 两个子孔径拼接的数学模型461
3.2.2 子孔径同步拼接模型与算法462
3.3 子孔径拼接迭代算法463
3.3.1 数学模型464
3.3.2 迭代算法468
3.3.3 大中型光学镜面的粗-精拼接策略471
3.4 子孔径划分方法471
3.4.1 子孔径的粗略划分472
3.4.2 计算子孔径的最佳拟合球474
3.4.3 子孔径划分的仿真验证477
3.5 子孔径拼接测量工作站482
3.5.1 子孔径拼接工作站的机械构型设计482
3.5.2 子孔径拼接工作站的运动学模型485
3.6 子孔径拼接测量的实验验证487
3.6.1 平面镜拼接测量实例487
3.6.2 球面镜拼接测量实例492
3.6.3 非球面镜拼接测量实例496
3.7 子孔径拼接测量方法的发展趋势499
附录A 线性化位形优化子问题的推导501
附录B 线性最小二乘问题的分块顺序QR分解程序504
参考文献505
第四章 大中型光学镜面相位恢复在位检测技术508
4.1 相位恢复检测技术综述508
4.1.1 相位恢复在位检测技术的意义508
4.1.2 相位恢复方法应用综述509
4.1.3 相位恢复算法理论综述511
4.2 相位恢复测量的基本原理和算法513
4.2.1 相位恢复测量原理513
4.2.2 光场衍射传播计算516
4.2.3 镜面检测相位恢复算法517
4.3 球面波的相位恢复检测522
4.3.1 测量装置522
4.3.2 口径200mm球面镜的测量522
4.3.3 大口径球面镜的测量527
4.4 亚像素分辨率相位恢复测量研究531
4.4.1 亚像素分辨率相位恢复测量原理531
4.4.2 亚像素光强约束函数设计534
4.4.3 亚像素分辨率镜面测量实验536
4.5 非球面镜的相位恢复检测技术539
4.5.1 非球面面形方程和非球面度539
4.5.2 非球面镜离焦光场特性540
4.5.3 非球面相位恢复测量规划542
4.5.4 APR算法设计544
4.6 非球面镜相位恢复测量实验548
4.6.1 光源和图像定位548
4.6.2 定位误差对测量的影响549
4.6.3 镜面遮光误差对测量的影响和控制方法551
4.6.4 口径170mm抛物面镜的检测551
参考文献554
第五章 光学零件制造中的亚表面质量检测与保障558
5.1 亚表面质量概述558
5.1.1 亚表面质量的概念558
5.1.2 亚表面质量对光学零件使用性能的影响559
5.2 亚表面损伤的产生机理563
5.2.1 磨削和研磨损伤产生机理563
5.2.2 抛光损伤产生机理565
5.3 磨削和研磨亚表面损伤检测技术568
5.3.1 损伤性检测技术568
5.3.2 无损检测技术572
5.3.3 亚表面损伤检测实验研究576
5.3.4 基于表面质量关联的亚表面检测技术研究581
5.4 亚表面损伤表征方法590
5.4.1 磨削过程590
5.4.2 研磨过程591
5.5 亚表面损伤深度预测方法596
5.5.1 磨削过程亚表面损伤深度预测596
5.5.2 研磨过程亚表面损伤深度预测598
5.6 加工参数对亚表面损伤深度的影响规律研究602
5.6.1 磨削过程参数对亚表面裂纹深度的影响602
5.6.2 研磨过程参数对亚表面裂纹深度的影响604
5.7 亚表面质量保障技术607
5.7.1 抛光亚表面损伤的表现形式607
5.7.2 抛光亚表面损伤检测610
5.7.3 抛光亚表面损伤模型616
5.7.4 传统抛光亚表面损伤的抑制策略617
5.7.5 复合加工及后处理技术提高激光损伤阈值620
参考文献624