图书介绍
实用机械加工工艺手册 第2版PDF|Epub|txt|kindle电子书版本网盘下载
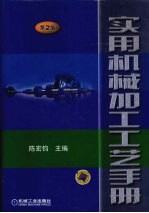
- 陈宏钧主编 著
- 出版社: 北京:机械工业出版社
- ISBN:7111113438
- 出版时间:2003
- 标注页数:1522页
- 文件大小:57MB
- 文件页数:1547页
- 主题词:
PDF下载
下载说明
实用机械加工工艺手册 第2版PDF格式电子书版下载
下载的文件为RAR压缩包。需要使用解压软件进行解压得到PDF格式图书。建议使用BT下载工具Free Download Manager进行下载,简称FDM(免费,没有广告,支持多平台)。本站资源全部打包为BT种子。所以需要使用专业的BT下载软件进行下载。如BitComet qBittorrent uTorrent等BT下载工具。迅雷目前由于本站不是热门资源。不推荐使用!后期资源热门了。安装了迅雷也可以迅雷进行下载!
(文件页数 要大于 标注页数,上中下等多册电子书除外)
注意:本站所有压缩包均有解压码: 点击下载压缩包解压工具
图书目录
第1章 机械制造常用名词术语1
1 机械制造工艺术语1
1.1 基本术语1
1.2 典型表面加工术语1
1.3 冷作、钳工及装配常用术语9
1.4 热处理名词术语11
2 机械制造工艺管理名词术语17
2.1 工艺管理术语17
2.2 工艺装备管理术语17
2.3 质量管理和质量保证术语18
2.4 定置管理术语22
第2章 机械加工工艺规程的设计23
第1节 机械加工工艺规程的编制23
1 机械加工工艺规程的作用23
2 机械加工工艺过程的组成23
3 机械加工工艺规程的制订23
3.1 工艺规程制订原则23
3.2 制订工艺规程所需原始资料23
3.3 工艺规程制订程序24
4 工艺过程设计中应考虑的主要问题24
4.1 定位基准选择24
4.2 零件表面加工方法的选择25
4.2.1 加工方法选择的原则25
4.2.2 各类表面的加工方案及适用范围25
4.3 加工顺序的安排27
4.3.1 加工阶段的划分27
4.3.2 工序的合理组合27
4.3.3 加工顺序的安排27
5 工序设计28
5.1 工序基准的选择28
5.2 工序尺寸的确定28
5.2.1 确定工序尺寸的方法28
5.2.2 工艺尺寸链的计算参数与计算公式28
5.2.3 工艺尺寸链的基本类型与工序尺寸的计算30
5.3 加工余量的确定36
5.4 机床的选择37
5.5 工艺装备的选择38
5.6 切削用量的选择38
5.7 时间定额的组成38
6 工艺文件格式及填写规则38
6.1 机械加工工艺过程卡片格式及填写规则38
6.2 机械加工工序卡片填写及格式规则40
6.3 标准零件(或典型零件)工艺过程卡片格式40
第2节 零件图样的工艺性审查43
1 各种加工类型对零件结构工艺性的要求43
1.1 对铸造零件结构工艺性的要求43
1.2 对锻造零件结构工艺性的要求43
1.3 对冲压零件结构工艺性的要求43
1.4 对焊接零件结构工艺性的要求43
1.5 对热处理零件结构工艺性的要求43
1.6 对切削加工零件结构工艺性的要求43
1.7 对装配零件结构工艺性的要求43
2 零件结构的切削加工工艺性43
2.1 工件便于在机床或夹具上装夹的图例43
2.2 减少装夹次数的图例43
2.3 减少刀具调整与走刀次数的图例43
2.4 采用标准刀具减少刀具种类的图例43
2.5 减少切削加工难度的图例43
2.6 减少加工量的图例51
2.7 加工时便于进刀、退刀和测量的图例51
2.8 保证零件在加工时的刚度的图例51
2.9 有利于改善刀具切削条件与提高耐用度的图例51
第3节 典型零件机械加工工艺过程举例55
1 单拐曲轴55
2 钻床主轴58
3 连杆60
4 丝杠64
5 铜套65
6 轴承套66
7 活塞67
8 矩形齿花键轴68
9 齿轮69
10 C6150车床主轴箱箱体70
第3章 机械加工质量73
第1节 机械加工精度73
1 影响加工精度的因素及改善措施73
1.1 影响尺寸精度的因素及改善措施73
1.2 影响形状精度的因素及改善措施73
1.3 影响位置精度的因素及改善措施73
2 各种加工方法的加工误差76
3 机械加工的经济精度77
3.1 加工路线与所能达到的加工精度和表面粗糙度77
3.2 各种加工方法能达到的尺寸经济精度77
3.3 各种加工方法能达到的形状经济精度83
3.4 各种加工方法能达到的位置经济精度83
第2节 机械加工表面质量86
1 加工表面粗糙度86
1.1 各种加工方法能达到的表面粗糙度86
1.2 影响加工表面粗糙度的因素及改善措施87
1.3 表面粗糙度与加工精度和配合之间的关系87
1.4 各种连接表面的粗糙度90
2 加工硬化与残余应力90
2.1 加工表面层的冷作硬化90
2.2 残余应力92
3 机械加工中的振动92
3.1 强迫振动的特点、产生原因与消减措施92
3.2 自激振动(颤振)的特点、产生原因与消减措施92
第4章 材料及热处理94
第1节 钢94
1 钢的分类94
2 钢牌号表示方法94
2.1 牌号表示方法基本原则94
2.2 钢的名称及其符号95
2.3 钢牌号表示方法的举例96
3 常用钢的品种、性能和用途99
3.1 结构钢99
3.1.1 碳素结构钢99
3.1.2 优质碳素结构钢100
3.1.3 低合金高强度结构钢103
3.1.4 合金结构钢104
3.1.5 易切削结构钢115
3.1.6 非调质机械结构钢115
3.1.7 弹簧钢115
3.2 工具钢117
3.2.1 碳素工具钢117
3.2.2 合金工具钢118
3.2.3 高速工具钢121
3.3 轴承钢123
3.4 特种钢124
3.4.1 不锈钢124
3.4.2 耐热钢126
4 型钢127
4.1 热轧圆钢和方钢尺寸规格127
4.2 热轧六角钢和八角钢尺寸规格127
4.3 冷拉圆钢、方钢、六角钢尺寸规格129
4.4 热轧扁钢的尺寸规格130
4.5 优质结构钢冷拉扁钢的尺寸规格132
4.6 热轧等边角钢的尺寸规格132
4.7 热轧不等边角钢的尺寸规格135
4.8 热轧工字钢的尺寸规格138
4.9 热轧槽钢的尺寸规格139
5 钢板和钢带140
5.1 热轧钢板和钢带140
5.2 冷轧钢板和钢带142
5.3 不锈钢热轧钢板143
5.4 不锈钢冷轧钢板144
5.5 锅炉用钢板的牌号、板厚及力学和工艺性能146
5.6 压力容器用钢板的牌号、板厚及力学和工艺性能146
6 钢管147
6.1 无缝钢管147
6.2 结构用无缝钢管154
6.3 结构用不锈钢无缝钢管154
6.4 不锈钢冷拔(轧)小直径无缝钢管的尺寸规格157
7 钢丝158
7.1 高速工具钢丝158
7.2 碳素弹簧钢丝159
7.3 合金弹簧钢丝159
7.4 油淬火—回火碳素弹簧钢丝160
7.5 油淬火—回火硅锰合金弹簧钢丝160
8 钢材的标记161
8.1 钢材标记代号161
8.2 钢材的涂色标记161
第2节 铸钢162
1 一般工程用铸造碳钢162
1.1 一般工程用铸造碳钢牌号及力学性能162
1.2 一般工程用铸造碳钢的特性和应用162
2 焊接结构用碳素钢铸件163
3 合金铸钢件163
3.1 合金铸钢的牌号及力学性能163
3.2 合金铸钢的用途164
4 高锰钢铸件的牌号、力学性能和适用范围165
5 工程结构用中、高强度不锈钢铸件165
5.1 工程结构用中、高强度不锈钢铸件的牌号及力学性能165
5.2 工程结构用中、高强度不锈钢铸件的特性和应用165
6 耐热钢铸件166
6.1 耐热钢铸件的牌号及力学性能166
6.2 耐热钢铸件的特性和应用166
第3节 铸铁167
1 灰铸铁167
2 球墨铸铁167
3 可锻铸铁169
4 蠕墨铸铁170
5 耐热铸铁171
6 高硅耐蚀铸铁172
7 耐磨铸铁172
8 抗磨白口铸铁172
第4节 非铁金属及其合金173
1 非铁金属及其合金产品代号表示方法173
2 铜及铜合金175
2.1 加工铜的牌号、代号及主要特性和应用举例175
2.2 加工黄铜的牌号、代号及主要特性和应用举例175
2.3 加工青铜的牌号、代号及主要特性和应用举例175
2.4 加工白铜的牌号、代号及主要特性和应用举例181
2.5 铜及铜合金力学性能182
2.6 铜及铜合金工艺性能184
3 铸造铜合金及铸造铜基轴承合金185
3.1 铸造铜合金185
3.2 铸造铜基轴承合金189
4 铝及铝合金190
4.1 变形铝及铝合金的新旧牌号对照190
4.2 常用铝及铝合金加工产品的牌号及主要特性和应用举例191
4.3 铝及铝合金热处理工艺参数195
5 铸造铝合金196
5.1 铸造铝合金的牌号、代号和力学性能196
5.2 铸造铝合金的主要特性和应用举例199
5.3 铸造铝合金热处理工艺规范201
第5节 粉末冶金材料201
5.1 粉末冶金材料的分类及应用举例201
5.2 粉末冶金减摩材料202
5.3 粉末冶金铁基结构材料203
5.4 粉末冶金多孔材料204
5.5 粉末冶金摩擦材料205
第6节 非金属材料206
6.1 常用工程塑料的性能特点及应用206
6.2 常用橡胶的特性及用途208
第7节 热处理210
1 热处理工艺分类及代号210
2 热处理工艺规范210
2.1 退火与正火工艺守则210
2.1.1 准备工作210
2.1.2 工艺规范211
2.1.3 加热设备212
2.1.4 操作方法及注意事项212
2.1.5 常见的缺陷及解决方法213
2.2 调质工艺守则213
2.2.1 准备工作213
2.2.2 工艺规范213
2.2.3 设备使用规范215
2.2.4 操作方法及注意事项216
2.2.5 一般低碳钢工夹具及吊具的强度计算216
2.3 淬火、回火工艺守则216
2.3.1 准备工作216
2.3.2 工艺规范217
2.3.3 设备使用规范219
2.3.4 操作方法及注意事项221
2.3.5 常见缺陷产生的原因及解决方法221
2.3.6 辅助工序的工艺设备与操作方法222
2.4 火焰淬火工艺守则223
2.4.1 准备工作223
2.4.2 工艺规范223
2.4.3 操作方法及注意事项223
2.4.4 常见缺陷产生原因及解决方法224
2.5 高频感应加热淬火、回火工艺守则224
2.5.1 准备工作224
2.5.2 工艺规范225
2.5.3 设备使用规范226
2.5.4 操作方法及注意事项227
2.5.5 常见缺陷产生原因及解决方法227
2.6 气体渗碳工艺守则227
2.6.1 准备工作227
2.6.2 工艺规范228
2.6.3 操作方法及注意事项229
2.6.4 设备230
2.6.5 常见缺陷产生原因及解决方法230
2.7 气体渗氮工艺守则230
2.7.1 渗氮前的热处理230
2.7.2 准备工作230
2.7.3 工艺规范231
2.7.4 渗氮设备及参数测量231
2.7.5 操作方法及注意事项232
2.7.6 常见缺陷产生原因及解决方法232
2.8 碱性发蓝工艺守则232
2.8.1 准备工作232
2.8.2 工艺规范233
2.8.3 发蓝后的补充处理234
2.8.4 常见缺陷产生原因及解决方法235
第5章 机械零件236
第1节 螺纹236
1 普通螺纹236
1.1 普通螺纹基本牙型236
1.2 普通螺纹直径与螺距系列236
1.3 普通螺纹基本尺寸238
1.4 普通螺纹公差与配合244
1.4.1 普通螺纹公差带245
1.4.2 内、外螺纹基本偏差245
1.4.3 公差带的大小及公差等级的划分245
1.4.4 内、外螺纹各直径的公差等级246
1.4.5 螺纹旋合长度248
1.4.6 螺纹精度及公差带的选用249
1.4.7 普通螺纹的极限偏差250
1.5 普通螺纹代号与标记268
2 梯形螺纹269
2.1 梯形螺纹牙型269
2.2 梯形螺纹直径与螺距表269
2.3 梯形螺纹基本尺寸270
2.4 梯形螺纹公差274
2.5 梯形螺纹代号和标记280
3 锯齿形螺纹281
3.1 锯齿形(3°、30°)螺纹牙型281
3.2 锯齿形螺纹的直径与螺距系列281
3.3 锯齿形螺纹基本尺寸281
3.4 锯齿形螺纹公差284
3.5 锯齿形螺纹标记288
4 管螺纹288
4.1 用螺纹密封的管螺纹(55°牙型角)288
4.1.1 牙型及要素名称代号288
4.1.2 螺纹的基本尺寸289
4.1.3 螺纹公差290
4.1.4 螺纹代号及标记示例290
4.2 非螺纹密封的管螺纹(55°牙型角)291
4.2.1 牙型及牙型尺寸计算291
4.2.2 基本尺寸和公差291
4.2.3 螺纹代号及标记示例291
4.3 60 °圆锥管螺纹293
4.3.1 螺纹术语及代号293
4.3.2 螺纹牙型及牙型尺寸293
4.3.3 60°圆锥管螺纹基本尺寸293
4.3.4 60°圆锥管螺纹公差294
4.3.5 螺纹代号及标记示例295
4.4 米制锥螺纹295
4.4.1 螺纹牙型295
4.4.2 基本尺寸295
4.4.3 米制锥螺纹公差296
4.4.4 螺纹代号及标记示例296
5 英制螺纹296
5.1 英制螺纹基本牙型及尺寸计算296
5.2 英制螺纹基本尺寸297
5.3 英制螺纹公差298
第2节 渐开线齿轮299
1 渐开线齿轮基本齿廓及模数系列299
1.1 齿轮基本齿廓299
1.2 齿轮模数系列299
1.3 模数、径节对照表299
2 渐开线圆柱齿轮300
2.1 直齿轮300
2.2 斜齿轮301
2.3 直齿条302
2.4 变位直齿圆柱齿轮几何计算302
2.5 齿轮精度303
2.5.1 齿轮和齿轮副误差及侧隙的定义和代号303
2.5.2 齿轮的公差组307
2.5.3 齿轮公差值308
3 直齿锥齿轮310
3.1 直齿锥齿轮几何尺寸计算310
3.2 锥齿轮精度312
3.2.1 锥齿轮、锥齿轮副的误差与侧隙312
3.2.2 锥齿轮及锥齿轮副公差316
4 圆柱蜗杆和蜗轮327
4.1 圆柱蜗杆的基本齿廓327
4.2 圆柱蜗杆和蜗轮的计算328
4.2.1 圆柱蜗杆传动几何尺寸计算328
4.2.2 蜗杆模数330
4.2.3 蜗杆分度圆直径d1标准值330
4.2.4 蜗杆分度圆上的导程角γ330
4.2.5 蜗杆头数z1与蜗轮齿数z2的推荐值330
4.3 圆柱蜗杆、蜗轮精度330
4.3.1 蜗杆、蜗轮及其传动的误差和侧隙330
4.3.2 蜗杆、蜗轮及其传动的公差335
第3节 键、花键和销342
1 键342
1.1 平键342
1.2 薄型平键344
1.3 半圆键形式和规格尺寸344
1.4 键和键槽的尺寸公差346
1.5 楔键347
1.6 切向键348
2 花键350
2.1 花键连接的类型、特点和应用350
2.2 矩形花键350
2.2.1 矩形花键尺寸系列350
2.2.2 矩形花键的公差与配合353
2.2.3 矩形花键的表面粗糙度Ra354
2.2.4 标记示例354
3 销354
3.1 销的类型及应用范围354
3.2 常用销的规格尺寸356
第4节 链和链轮360
1 滚子链传动360
1.1 滚子链的结构形式和规格尺寸360
1.2 滚子链用附件360
2 滚子链链轮363
2.1 滚子链链轮齿槽形状363
2.2 三圆弧一直线齿槽形状和尺寸计算363
2.3 滚子链链轮轴向齿廓及尺寸364
2.4 滚子链链轮的基本参数和主要尺寸364
2.5 链轮公差364
2.6 滚子链链轮常用材料及热处理366
第5节 滚动轴承366
1 滚动轴承的分类366
2 滚动轴承代号的构成367
2.1 基本代号367
2.2 前置、后置代号372
2.3 轴承代号示例375
3 常用滚动轴承型号及外形尺寸举例375
3.1 深沟球轴承375
3.2 调心球轴承378
3.3 双列圆柱滚子轴承379
3.4 圆锥滚子轴承381
3.5 双列圆锥滚子轴承382
3.6 角接触球轴承383
3.7 推力球轴承386
4 滚动轴承的配合387
第6节 圆锥和棱体388
1 锥度、锥角及其公差388
1.1 圆锥的术语及定义388
1.2 锥度与锥角系列388
1.2.1 一般用途圆锥的锥度与锥角388
1.2.2 特殊用途圆锥的锥度与锥角389
1.3 圆锥公差390
1.3.1 圆锥直径公差所能限制的最大圆锥角误差390
1.3.2 圆锥角公差AT391
2 棱体392
2.1 棱体的术语及定义392
2.2 棱体的角度与斜度系列392
第7节 常用零件结构要素394
1 中心孔394
1.1 60°中心孔394
1.2 75°、90°中心孔394
2 各类槽395
2.1 退刀槽395
2.1.1 外圆退刀槽及相配件的倒角和倒圆395
2.1.2 公称直径相同具有不同配合的退刀槽397
2.1.3 带槽孔的退刀槽397
2.2 砂轮越程槽397
2.3 润滑槽399
2.4 T形槽400
2.5 燕尾槽402
3 零件倒圆与倒角402
4 球面半径403
5 螺纹零件403
5.1 紧固件外螺纹零件的末端403
5.2 普通螺纹的收尾、肩距、退刀槽和倒角尺寸404
5.3 普通内螺纹的收尾、肩距、退刀槽和倒角尺寸405
5.4 普通螺纹的内、外螺纹余留长度、钻孔余留深度和螺栓突出螺母的末端长度405
5.5 紧固件用通孔和沉孔408
5.6 梯形螺纹的收尾、退刀槽和倒角尺寸410
5.7 米制锥螺纹的结构要素410
5.8 圆柱管螺纹的收尾、退刀槽和倒角尺寸412
第6章 机械加工工序间加工余量414
1 装夹及下料尺寸余量414
1.1 棒材、板材及焊接后的板材结构件各部分加工余量示意414
1.2 夹持长度及夹紧余量414
1.3 下料尺寸余量414
1.3.1 切断余量415
1.3.2 切断刀具切出的切口宽度415
1.3.3 棒材外径和端面的切削加工余量415
1.3.4 板材厚度和端面的切削加工余量420
1.3.5 板材焊接后经切削加工的板材厚度和端面加工余量422
2 轴的加工余量424
2.1 外圆柱表面加工余量及偏差424
2.2 轴端面加工余量及公差426
2.3 槽的加工余量及公差427
3 内孔加工余量及偏差428
4 平面加工余量及偏差430
5 切除渗碳层的加工余量431
6 非铁金属及其合金的加工余量432
7 齿轮和花键的精加工余量435
8 攻螺纹前底孔直径和套螺纹前圆杆直径尺寸的确定437
第7章 金属切削机床及辅具440
第1节 金属切削机床型号编制方法440
1 通用机床型号表示方法440
1.1 型号表示方法440
1.2 机床的分类及类代号440
1.3 机床的特性代号440
1.4 机床的组、系代号及主参数441
1.5 通用机床的设计顺序号441
1.6 主轴数和第二主参数的表示方法441
1.7 机床的重大改进顺序号441
1.8 其他特性代号及其表示方法441
1.9 企业代号及其表示方法441
1.10 金属切削机床统一名称和类、组、系划分441
2 专用机床的型号441
3 机床自动线的型号441
第2节 通用机床技术参数与辅具455
1 车床455
1.1 常用车床的型号与技术参数455
1.1.1 卧式车床的型号与技术参数455
1.1.2 马鞍车床的型号与技术参数455
1.1.3 立式车床的型号与技术参数455
1.1.4 转塔车床、回轮车床的型号与技术参数455
1.1.5 仿形车床的型号与技术参数455
1.1.6 曲轴车床的型号与技术参数455
1.1.7 数控卧式车床的型号与技术参数455
1.2 普通车床辅具465
1.2.1 刀杆465
1.2.2 刀夹468
1.2.3 加工螺纹用辅具469
2 铣床470
2.1 常用铣床的型号与技术参数470
2.1.1 卧式升降台铣床的型号与技术参数470
2.1.2 万能升降台铣床的型号与技术参数470
2.1.3 立式升降台铣床、数控立式升降台铣床的型号与技术参数470
2.1.4 工具铣床、数控工具铣床的型号与技术参数470
2.1.5 龙门铣床的型号与技术参数470
2.2 铣床辅具477
2.2.1 中间套477
2.2.2 铣刀杆480
2.2.3 铣夹头491
3 钻床493
3.1 常用钻床的型号与技术参数493
3.1.1 台式钻床的型号与技术参数493
3.1.2 立式钻床的型号与技术参数493
3.1.3 摇臂钻床的型号与技术参数493
3.1.4 深孔钻床的型号与技术参数493
3.2 钻床铺具497
3.2.1 过渡套、接长套、夹紧套497
3.2.2 接杆502
3.2.3 刀杆505
3.2.4 夹头510
3.2.5 扁尾锥柄用楔513
4 镗床513
4.1 常用镗床的型号与技术参数513
4.1.1 卧式铣镗床的型号与技术参数513
4.1.2 数控卧式镗床的型号与技术参数513
4.1.3 落地镗床、数控落地铣镗床的型号与技术参数513
4.1.4 坐标镗床的型号与技术参数513
4.1.5 精镗床的型号与技术参数513
4.2 镗床辅具518
4.2.1 镗刀杆518
4.2.2 镗杆530
4.2.3 镗刀架531
4.2.4 接杆533
4.2.5 镗套与衬套535
4.2.6 其他539
5 磨床540
5.1 常用磨床的型号与技术参数540
5.1.1 万能外圆磨床的型号与技术参数540
5.1.2 无心外圆磨床的型号与技术参数540
5.1.3 内圆磨床的型号与技术参数540
5.1.4 卧轴矩台平面磨床的型号与技术参数540
5.1.5 立轴矩台平面磨床的型号与技术参数540
5.1.6 卧轴圆台平面磨床的型号与技术参数540
5.1.7 立轴圆台平面磨床的型号与技术参数540
5.1.8 万能工具磨床的型号与技术参数540
5.1.9 曲轴磨床的型号与技术参数540
5.1.10 花键轴磨床的型号与技术参数540
5.1.11 珩磨机的型号与技术参数540
5.2 磨床辅具569
5.2.1 顶尖569
5.2.2 接杆及螺钉569
6 拉床572
6.1 常用拉床的型号与技术参数572
6.1.1 立式拉床的型号与技术参数572
6.1.2 卧式拉床的型号与技术参数572
6.2 拉床辅具573
6.2.1 接头573
6.2.2 夹头、扳手574
6.2.3 导套、垫片及支座577
7 齿轮加工机床582
7.1 常用齿轮加工机床的型号与技术参数582
7.1.1 滚齿机的型号与技术参数582
7.1.2 插齿机的型号与技术参数588
7.1.3 剃齿机的型号与技术参数589
7.1.4 花键轴铣床的型号与技术参数589
7.2 齿轮加工机床辅具591
7.2.1 滚齿刀杆591
7.2.2 刀垫592
7.2.3 接套592
8 螺纹加工机床593
8.1 专用螺纹车床的型号与技术参数593
8.2 螺纹铣床的型号与技术参数593
8.3 螺纹磨床的型号与技术参数593
8.4 攻丝机的型号与技术参数593
8.5 滚丝机的型号与技术参数597
8.6 搓丝机的型号与技术参数597
9 刨床与插床597
9.1 常用刨床、插床的型号与技术参数597
9.1.1 牛头刨床的型号与技术参数597
9.1.2 单臂刨床的型号与技术参数597
9.1.3 龙门刨床、数控龙门刨床的型号与技术参数597
9.1.4 插床的型号与技术参数597
9.2 刨床辅具597
9.2.1 槽刨刀刀杆597
9.2.2 刨刀刀杆597
10 锯床600
10.1 带锯床的型号与技术参数600
10.2 圆锯床的型号与技术参数600
10.3 弓锯床的型号与技术参数600
第8章 机床夹具603
第1节 通用夹具603
1 顶尖603
2 卡盘、过渡盘和花盘605
3 鸡心夹头、卡环和拨盘614
4 分度头617
5 机床用平口虎钳618
6 常用回转工作台621
7 吸盘624
8 铣头、插头与镗头626
第2节 专用夹具628
1 机床夹具设计基本要求628
1.1 工件定位原理及其应用628
1.1.1 六点定位原理628
1.1.2 工件的定位要求629
1.1.3 常用定位方法和定位元件所能限制的自由度629
1.1.4 常见加工形式中应限制的自由度633
1.2 对夹紧装置的基本要求635
1.3 夹具的对定636
1.3.1 夹具对切削运动的定位636
1.3.2 夹具对刀具的定位638
1.3.3 夹具分度与转位的对定644
2 机床夹具常用标准零部件645
2.1 定位件645
2.2 导向件655
2.3 支承件663
2.4 夹紧件670
2.5 对刀件683
3 车床夹具的典型结构685
3.1 车床夹具的特点及设计要求685
3.2 车床夹具典型结构的技术要求686
3.3 车夹具类型结构举例688
3.3.1 心轴类688
3.3.2 卡盘类693
4 钻床夹具693
4.1 钻床夹具的特点和主要类型693
4.2 钻(镗)床夹具典型结构的技术要求696
4.3 钻夹具类型结构举例700
5 镗床夹具704
5.1 镗床夹具设计要点704
5.2 镗床夹具典型结构的技术要求704
5.3 镗床夹具类型结构举例704
6 铣床夹具706
6.1 铣床夹具典型结构的技术要求707
6.2 铣床夹具类型结构举例711
7 磨床夹具713
第3节 可调夹具715
1 可调整夹具的特点、适用范围与设计要点715
2 可调整夹具结构示例715
第4节 组合夹具716
1 组合夹具的使用范围与经济效果716
2 组合夹具的系列、元件类别及作用717
3 组合夹具典型结构举例719
3.1 钻夹具719
3.2 车夹具721
3.3 铣、刨夹具725
3.4 镗模725
3.5 组合夹具的扩大使用725
第9章 技术测量及量具729
第1节 测量与测量误差729
1 测量常用术语729
2 测量方法的分类729
3 测量误差的分类、产生原因及消除方法729
第2节 机械零件常规检测730
1 常用测量计算举例730
1.1 常用几何图形计算公式730
1.2 圆的几何图形计算732
1.3 内圆弧与外圆弧计算733
1.4 V形槽宽度、角度计算733
1.5 燕尾与燕尾槽宽度计算734
1.6 内圆锥与外圆锥计算734
2 形位误差的检测735
2.1 形位误差的检测原则735
2.2 直线度误差的常用测量方法736
2.3 平面度误差的常用测量方法737
2.4 圆度误差的常用测量方法738
2.5 轮廓度误差的常用测量方法739
2.6 定向误差的常用测量方法740
2.7 定位误差的常用测量方法743
2.8 跳动量的常用测量方法745
3 表面粗糙度的检测747
3.1 表面粗糙度的测量方法、特点及应用747
3.2 表面粗糙度标准器具747
3.2.1 表面粗糙度标准样块747
3.2.2 表面粗糙度比较样块748
4 螺纹的检测749
4.1 螺纹单项测量方法及测量误差749
4.2 三针测量方法749
4.3 单针测量方法753
4.4 综合测量方法754
5 齿轮检测754
5.1 公法线长度的测量754
5.1.1 标准直齿圆柱齿轮公法线长度测量754
5.1.2 斜齿圆柱齿轮公法线长度测量757
5.1.3 公法线平均长度偏差及公差759
5.2 分度圆弦齿厚的测量761
5.3 固定弦齿厚的测量762
5.4 齿厚上偏差及公差763
第3节 常用计量器具765
1 游标类量具765
2 螺旋测微量具767
3 机械式测微仪771
4 角度量具773
5 量块及量规778
第10章 刀具和磨料磨具800
第1节 刀具材料及刀片800
1 刀具切削部分的材料800
1.1 对刀具切削部分材料性能的要求800
1.2 常用刀具材料800
1.2.1 高速钢800
1.2.2 硬质合金803
1.2.3 陶瓷刀具材料810
1.2.4 超硬刀具材料811
2 刀片811
2.1 硬质合金焊接刀片811
2.1.1 常用焊接车刀刀片811
2.1.2 基本型硬质合金焊接刀片811
2.2 可转位硬质合金刀片817
2.2.1 可转位硬质合金刀片的标记方法817
2.2.2 带圆孔的可转位硬质合金刀片820
2.2.3 无孔可转位硬质合金刀片836
2.2.4 沉孔可转位硬质合金刀片836
2.2.5 硬质合金可转位铣刀片846
2.3 可转位陶瓷刀片的型号与基本参数850
第2节 车刀853
1 刀具切削部分几何角度及其选择853
1.1 刀具切削部分的几何角度853
1.1.1 刀具切削部分的组成853
1.1.2 确定刀具角度的三个辅助平面名称和定义853
1.1.3 刀具的切削角度及其作用854
1.1.4 车刀的工作角度854
1 .2 刀具切削部分几何参数的选择856
1.2.1 前角的选择856
1.2.2 车刀前面切削刃和刀尖形状的选择857
1.2.3 后角的选择858
1.2.4 主偏角的选择859
1.2.5 副偏角的选择859
1.2.6 刃倾角的选择859
1.2.7 过渡刃的选择860
2 车刀类型及规格尺寸860
2.1 高速钢车刀条860
2.2 焊接车刀862
2.2.1 硬质合金外表面车刀862
2.2.2 硬质合金内表面车刀868
2.3 可转位车刀871
2.3.1 可转位车刀刀片的夹固形式871
2.3.2 可转位车刀型号表示规则872
2.3.3 优先采用的形式和尺寸875
2.3.4 可转位内孔车刀892
2.4 机夹车刀900
2.4.1 机夹切断车刀900
2.4.2 机夹螺纹车刀903
第3节 孔加工刀具905
1 麻花钻905
1.1 标准麻花钻头的切削角度905
1.2 高速钢麻花钻的类型、规格范围及标准代号905
1.3 硬质合金麻花钻908
1.4 扩孔钻的类型、规格范围及标准代号909
1.5 锪钻的类型、规格范围及标准代号910
2 中心钻911
3 扁钻913
4 深孔钻913
4.1 单刃外排屑深孔钻(枪钻)913
4.2 双刃外排屑深孔钻913
4.3 单刃内排屑深孔钻915
4.4 多刃错齿内排屑深孔钻916
4.5 机夹可转位内排屑深孔钻的形式及加工范围917
4.6 BTA内排屑深孔钻的形式及加工范围918
4.7 喷吸钻的形式及尺寸系列918
4.8 DF系统深孔钻的形式及规格尺寸919
4.9 常用深孔套料钻的类型及特点920
5 铰刀921
5.1 铰刀的主要几何参数921
5.2 常用铰刀的形式和主要技术参数921
5.2.1 手用铰刀921
5.2.2 直柄机用铰刀921
5.2.3 锥柄机用铰刀924
5.2.4 硬质合金直柄机用铰刀926
5.2.5 硬质合金锥柄机用铰刀926
5.2.6 手用1:50锥度销子铰刀928
5.2.7 手用长刃1:50锥度销子铰刀929
5.2.8 锥柄机用1:50锥度销子铰刀930
5.2.9 直柄莫氏圆锥和米制圆锥铰刀930
5.2.10 锥柄莫氏圆锥和米制圆锥铰刀931
5.2.11 带刃倾角直柄机用铰刀932
5.2.12 带刃倾角锥柄机用铰刀933
5.2.13 套式机用铰刀934
5.2.14 可调节手用铰刀934
5.2.15 硬质合金可调节浮动铰刀934
5.2.16 米制锥螺纹锥孔铰刀934
第4节 铣刀939
1 铣刀切削部分的几何形状和角度选择939
2 常用铣刀的类型及规格尺寸942
2.1 立铣刀942
2.2 键槽铣刀947
2.3 T形槽铣刀949
2.4 半圆键槽铣刀951
2.5 直柄燕尾槽铣刀和直柄反燕尾槽铣刀952
2.6 槽铣刀953
2.7 锯片铣刀955
2.8 三面刃铣刀960
2.9 圆柱形铣刀969
2.10 铲背成形铣刀970
2.11 角度铣刀973
2.12 硬质合金可转位铣刀976
2.12.1 可转位立铣刀976
2.12.2 可转位三面刃铣刀977
2.12.3 可转位面铣刀977
第5节 螺纹刀具979
1 丝锥979
1.1 丝锥的结构和几何参数979
1.2 常用丝锥的规格范围及标准代号980
2 板牙987
2.1 板牙的类型和使用范围987
2.2 圆板牙的结构和几何参数988
2.3 管螺纹板牙的结构988
2.4 常用板牙的规格范围及标准代号989
3 普通螺纹滚丝轮的形式及规格尺寸990
4 普通螺纹用搓丝板形式及规格尺寸993
第6节 齿轮和花键刀具995
1 盘形齿轮铣刀的形式和基本尺寸995
2 盘形锥齿轮铣刀的形式和基本尺寸997
3 渐开线齿轮滚刀的形式和基本尺寸997
3.1 小模数齿轮滚刀997
3.2 齿轮滚刀998
3.3 镶片齿轮滚刀999
3.4 磨前齿轮滚刀1000
3.5 剃前齿轮滚刀1001
4 盘形剃齿刀的形式和主要尺寸1002
5 直齿插齿刀的形式和主要尺寸1004
5.1 盘形直齿插齿刀1004
5.2 碗形直齿插齿刀1006
5.3 锥柄直齿插齿刀1008
6 渐开线花键滚刀的形式和主要尺寸1009
6.1 30°压力角渐开线花键滚刀1009
6.2 45°压力角渐开线花键滚刀1009
7 矩形花键滚刀的形式和主要尺寸1010
第7节 拉刀1011
1 圆推刀的形式和主要尺寸1011
2 键槽拉刀1020
2.1 平刀体键槽拉刀的形式和主要尺寸1020
2.2 加宽平刀体键槽拉刀的形式和主要尺寸1020
2.3 带倒角齿键槽拉刀的形式和主要尺寸1024
第8节 磨料磨具1026
1 普通磨料磨具1026
1.1 普通磨料1026
1.1.1 磨料的品种、代号及应用范围1026
1.1.2 磨料粒度号及其选择1026
1.2 普通磨具1028
1.2.1 磨具硬度代号1028
1.2.2 磨具组织号及其适用范围1028
1.2.3 结合剂的代号、性能及其适用范围1028
1.2.4 磨具代号1028
1.2.5 普通磨具的标志方法1033
1.2.6 普通磨具的最高工作线速度1034
1.2.7 常用磨具的规格尺寸1034
2 超硬材料1044
2.1 超硬磨料的品种、代号及应用范围1044
2.2 粒度1044
2.3 超硬磨料结合剂及其代号、性能和应用范围1045
2.4 浓度代号1045
2.5 砂轮、油石及磨头的尺寸代号和术语1046
2.6 砂轮、油石及磨头的形状代号1046
2.7 标记示例1051
2.8 超硬材料制品的形状代号及主要用途1051
第11章 切削加工1052
第1节 车削加工1052
1 车床加工范围及装夹方法1052
1.1 卧式车床加工1052
1.1.1 卧式车床加工范围1052
1.1.2 卧式车床常用装夹方法1052
1.2 立式车床加工1052
1.2.1 立式车床加工范围1055
1.2.2 立式车床常用装夹方法1056
2 典型零件车削加工1056
2.1 车削圆锥面1056
2.1.1 锥体各部分尺寸的计算公式1056
2.1.2 车削圆锥面方法1056
2.1.3 车削圆锥面时小溜板转动角度举例1058
2.1.4 车标准锥度和常用锥度时小刀架和靠模板转动角度1059
2.2 车削成形面1060
2.2.1 成形面车削方法1060
2.2.2 常用成形刀(样板刀)类型及应用1061
2.3 车削球面1063
2.4 旋风车削椭圆轴和孔1065
2.5 车削偏心工件1066
2.5.1 车削偏心工件的装夹方法1066
2.5.2 车削曲轴的装夹方法1068
2.6 车削表面的滚压加工1069
2.6.1 加工方法1069
2.6.2 滚压加工常用工具及其应用1070
2.6.3 滚轮式滚压工具常用滚轮外圆形状及其应用1071
2.6.4 滚花1072
2.7车 削细长轴1073
2.7.1 细长轴的加工特点1073
2.7.2 细长轴的装夹1073
2.7.3 车削细长轴车刀几何参数及特点1075
2.7.4 车削细长轴常用切削用量1077
2.7.5 车削细长轴常见的工件缺陷和产生原因1077
2.8 车削薄壁工件1077
2.8.1 工件的装夹方法1077
2.8.2 刀具几何角度的选择1079
2.8.3 精车薄壁工件的切削用量1079
2.9 冷绕弹簧1079
2.9.1 卧式车床可绕制弹簧的种类1079
2.9.2 绕制圆柱形螺旋弹簧用心轴直径的计算1079
2.10 卧式车床加工常见问题的产生原因及解决方法1080
3 车削用量的选择1081
3.1 车刀的磨纯标准及耐用度1081
3.2 车削用量的选择1081
3.2.1 硬质合金及高速钢车刀粗车外圆和端面的进给量1081
3.2.2 硬质合金外圆车刀半精车的进给量1082
3.2.3 硬质合金及高速钢镗刀粗镗孔进给量1082
3.2.4 切断及切槽的进给量1084
3.2.5 成形车削时的进给量1084
3.2.6 用YT15硬质合金车刀车削碳钢、铬钢、镍铬钢及铸钢时的切削速度1084
3.2.7 用YG6硬质合金车刀车削灰铸铁时的切削速度1084
3.2.8 涂层硬质合金车刀的切削用量1086
3.2.9 陶瓷车刀的切削用量1086
3.2.10 立方氮化硼车刀的切削用量1088
3.2.11 金刚石车刀的切削用量1089
第2节 螺纹加工1090
1 车螺纹1090
1.1 对三角形螺纹车刀几何形状的要求1090
1.2 车螺纹车刀的刀尖宽度尺寸1090
1.3 车螺纹时的交换齿轮计算1090
1.3.1 无进给箱车床车螺纹交换齿轮计算1090
1.3.2 有进给箱车床车螺纹交换齿轮计算1093
1.4 螺纹车刀的安装1094
1.5 螺纹车削进刀方式1095
1.6 常用螺纹车刀的特点与应用1096
1.7 车多线螺纹分线方法1100
1.8 高速钢及硬质合金车刀车削不同材料螺纹的切削用量1102
1.9 高速钢车刀车削螺纹时常用切削液1102
1.10 车削螺纹常见问题、产生原因及解决方法1003
2 旋风铣削螺纹1104
2.1 旋风铣削螺纹方式及适用范围1104
2.2 旋风铣削螺纹的刀具材料和几何角度1105
2.3 旋风铣削螺纹常用切削用量1105
3 用板牙和丝锥切削螺纹1106
3.1 用车床套螺纹和攻螺纹的工具1106
3.2 攻螺纹和套螺纹时产生废品的原因及预防方法1106
第3节 铣削加工1106
1 铣削方式、铣削范围和基本方法1106
1.1 铣削方式1106
1.2 铣削范围和基本方法1108
2 分度头及分度方法1111
2.1 分度头传动系统及分度头定数1111
2.2 分度方法及计算1112
2.2.1 单式分度法计算及分度表1112
2.2.2 差动分度法计算及分度表1113
2.2.3 近似分度法计算及分度表1114
2.2.4 角度分度法计算及分度表1115
2.2.5 直线移距分度法1115
3 典型零件的铣削加工1116
3.1 铣削离合器1116
3.1.1 齿式离合器的种类及特点1116
3.1.2 齿式离合器的铣削及计算1118
3.1.3 分度头扳角1119
3.2 铣削凸轮1121
3.2.1 凸轮传动的三要素1122
3.2.2 等速圆盘凸轮的铣削1122
3.2.3 等速圆柱凸轮的铣削1123
3.3 铣削球面的方法1124
3.4 铣刀、麻花钻头和铰刀的加工1125
3.4.1 前角γo=0°的铣刀开齿1125
3.4.2 前角γo>0°的铣刀开齿1125
3.4.3 圆柱螺旋齿铣刀的开齿1125
3.4.4 端面齿的铣削1128
3.4.5 锥面齿铣削1128
3.4.6 麻花钻头槽的铣削1129
3.4.7 铰刀的开齿1129
3.5 铣削加工常见问题产生原因及解决方法1130
4 铣削用量的选择1131
4.1 铣刀磨钝标准及耐用度1131
4.2 铣削用量1132
4.2.1 高速钢端铣刀、圆柱形铣刀和圆盘铣刀铣削时的进给量1132
4.2.2 高速钢立铣刀、角铣刀、半圆铣刀、切槽铣刀和切断铣刀铣削钢的进给量1133
4.2.3 硬质合金端铣刀、圆柱形铣刀和圆盘铣刀铣削平面和凸台的进给量1134
4.2.4 硬质合金立铣刀铣削平面和凸台的进给量1135
4.2.5 铣削速度1135
第4节 齿轮加工1136
1 各种齿轮加工方法1136
2 成形法铣削齿轮1140
2.1 铣刀号数的选择1140
2.2 齿坯加工精度1140
2.3 铣削直齿条、斜齿条1141
2.4 铣斜齿圆柱齿轮1143
2.4.1 斜齿轮的当量齿数1143
2.4.2 查图表方法选择铣刀号数1144
2.4.3 铣斜齿圆柱齿轮交换齿轮计算1144
2.4.4 工作台、工件的旋转角度及方向1144
2.4.5 铣削时应注意的事项1145
2.5 铣直齿锥齿轮1145
2.5.1 选择铣刀号数1145
2.5.2 铣削方法1145
3 飞刀展成铣蜗轮1146
3.1 铣削方法1146
3.2 交换齿轮计算1146
3.3 飞刀各部尺寸计算公式1146
4 滚齿1149
4.1 滚齿机传动系统1149
4.2 常用滚齿机连接尺寸1149
4.2.1 滚齿机主要相关尺寸1149
4.2.2 工作台尺寸1149
4.2.3 刀架及尾架尺寸1150
4.3 常用滚齿夹具及齿轮的安装1150
4.4 滚刀心轴和滚刀的安装要求1151
4.5 滚刀精度的选用1151
4.6 滚齿工艺参数的选择1151
4.7 滚齿调整1152
4.7.1 交换齿轮计算及滚齿机定数1152
4.7.2 滚刀安装角度和工作台转动方向及中间轮设置1152
4.8 滚切大质数齿轮1156
4.8.1 滚切大质数直齿圆柱齿轮时各组交换齿轮计算1156
4.8.2 滚切大质数斜齿圆柱齿轮时各组交换齿轮计算1156
4.8.3 Y38滚齿机加工大质数直齿圆柱齿轮时,分度、差动交换齿轮表1157
4.8.4 p的推荐值1157
4.9 滚齿加工常见缺陷及解决方法1157
5 挂轮表1160
6 插齿1164
6.1 插齿机的组成及传动系统1164
6.2 插齿机的基本参数和工作精度1165
6.2.1 插齿机的基本参数1165
6.2.2 常用插齿机的工作精度1166
6.3 常用插齿机连接尺寸1166
6.4 插齿刀的调整1167
6.5 插齿用夹具及调整1169
6.6 常用插齿机交换齿轮计算1170
6.7 插削余量及插削用量的选用1170
6.8 插齿加工中常出现的缺陷及解决方法1171
7 剃齿1173
7.1 剃齿机及其精度要求1173
7.2 剃齿刀的基本尺寸1174
7.3 剃齿用心轴1174
7.4 剃齿的切削用量1175
7.5 剃齿加工余量1176
7.6 剃齿方法1176
7.6.1 剃齿机与刀、夹具的调整精度1176
7.6.2 轴交角的调整1177
7.6.3 常用的剃齿方法1177
7.7 剃齿误差与轮齿接触区偏差1178
7.7.1 剃齿误差产生原因及解决方法1178
7.7.2 轮齿接触区的偏差与修正方法1179
第5节 花键、链轮加工1179
1 花键的加工1179
1.1 花键的定心方式及加工精度1179
1.2 在铣床上铣削矩形齿花键轴1180
1.2.1 用单刀铣削矩形齿花键轴1180
1.2.2 用组合铣刀铣削矩形齿花键轴1182
1.2.3 用硬质合金组合刀盘精铣花键轴1182
1.2.4 用成形铣刀铣削花键轴1182
1.3 铣削花键轴时产生误差的原因及解决方法1183
2 铣削链轮1184
2.1 铣削滚子链链轮1184
2.1.1 直线端面齿形滚子链链轮主要尺寸及计算公式1184
2.1.2 直线端面齿形滚子链链轮铣削方法1184
2.1.3 滚子链链轮的测量1186
2.1.4 链轮工作图标注要求1187
2.2 铣削齿形链链轮1187
2.2.1 用单角度铣刀铣削1187
2.2.2 用三面刃铣刀铣削1187
2.2.3 齿形链链轮的测量1187
第6节 磨削加工1189
1 磨削加工基础1189
1.1 砂轮平衡与修整1189
1.1.1 砂轮安装与静平衡1189
1.1.2 砂轮修整方法1189
1.2 常用磨削液的名称及性能1189
2 普通磨削1189
2.1 外圆磨削1189
2.1.1 外圆磨削常用方法1194
2.1.2 外圆磨削余量1194
2.1.3 外圆磨削切削用量的选择1196
2.1.4 外圆磨削常见的工件缺陷、产生原因及解决方法1199
2.2 内圆磨削1200
2.2.1 内圆磨削常用方法1200
2.2.2 内圆磨削余量的合理选择1201
2.2.3 内圆磨削切削用量的选择1201
2.2.4 内圆磨削常见的工件缺陷、产生原因及解决方法1206
2.3 平面磨削1206
2.3.1 平面磨削常用方法1206
2.3.2 平面磨削余量的合理选择1209
2.3.3 平面磨削切削用量的选择1210
2.3.4 平面磨削常见的工件缺陷、产生原因及解决方法1213
2.4 无心磨削1214
2.4.1 无心外圆磨削常用方法1214
2.4.2 无心外圆磨削切削用量的选择1214
2.4.3 无心外圆磨削常见的工件缺陷、产生原因及解决方法1216
2.5 成形磨削的几种方法1218
3 高效与低粗糙度磨削1219
3.1 高速磨削1219
3.1.1 高速磨削的特点1219
3.1.2 高速磨削对机床的要求1219
3.1.3 高速磨削对砂轮的要求1220
3.1.4 高速外圆磨削钢件的磨削用量1220
3.2 宽砂轮磨削1220
3.2.1 宽砂轮磨削的特点1220
3.2.2 宽砂轮磨削对机床的要求1220
3.2.3 宽砂轮磨削砂轮的选择1220
3.2.4 宽砂轮磨削工艺参数的选择1221
3.3 低粗糙度磨削1221
3.3.1 低粗糙度磨削分类1221
3.3.2 低粗糙度磨削砂轮的选择1222
3.3.3 低粗糙度磨削对机床的要求1222
3.3.4 各种磨削方式低粗糙度磨削的工艺参数1222
4 刀具刃磨1224
4.1 刀具刃磨用砂轮的选择1224
4.1.1 刃磨刀具的名称及砂轮的选择1224
4.1.2 刃磨一般刀具时砂轮形状与外径的选择1224
4.2 砂轮和支片安装位置的确定1224
4.3 刀具刃磨实例1227
4.3.1 铣刀刃磨1227
4.3.2 拉刀刃磨1229
第7节 光整加工1230
1 研磨1230
1.1 研磨的分类和适用范围1230
1.2 研磨剂1230
1.2.1 常用磨料及适用范围1230
1.2.2 磨料粒度的选择1231
1.2.3 研磨液1231
1.2.4 研磨剂配制1232
1.3 研具1232
1.3.1 研具材料1233
1.3.2 通用研具1233
1.4 研磨方法1236
1.4.1 常用研磨运动轨迹1236
1.4.2 研具的压砂1236
1.4.3 研磨工艺参数的选择1237
1.4.4 研磨实例要点1238
1.5 研磨常见问题1239
1.5.1 平板压砂常见问题及产生原因1239
1.5.2 研磨时常见弊病形式及产生原因1240
2 珩磨1240
2.1 珩磨头结构及连接方式1240
2.1.1 常用珩磨头结构形式1240
2.1.2 珩磨头的连接方式1240
2.2 珩磨用夹具1242
2.2.1 珩磨加工常用夹具结构形式1242
2.2.2 珩磨加工中的对中1243
2.3 珩磨油石的选择1245
2.3.1 珩磨油石磨料的选择1245
2.3.2 珩磨油石磨料粒度的选择1246
2.3.3 珩磨油石硬度的选择1246
2.3.4 结合剂的选择1246
2.3.5 组织和浓度的选择1246
2.3.6 珩磨油石长度的选择1246
2.3.7 珩磨油石数量和宽度的选择1247
2.4 珩磨工艺参数的选择1247
2.4.1 珩磨速度和珩磨交叉角1247
2.4.2 珩磨油石的工作压力1247
2.4.3 珩磨油石的行程1247
2.4.4 珩磨余量的选择1248
2.4.5 珩磨液的选择1248
2.4.6 对工件珩磨前的要求1248
2.5 珩磨缺陷产生原因及解决方法1249
3 抛光1252
3.1 抛光轮材料的选用1252
3.2 磨料和抛光剂1252
3.2.1 软磨料的种类和特性1252
3.2.2 固体抛光剂的种类与用途1252
3.3 抛光工艺参数1253
第8节 钻削、扩削、铰削加工1253
1 钻削1253
1.1 典型钻头举例1253
1.1.1 群钻1253
1.1.2 几种典型钻头举例1259
1.2 钻削方法1261
1.2.1 钻削不同孔距精度所用的加工方法1261
1.2.2 切削液的选用1261
1.2.3 常用钻孔方法1261
1.2.4 特殊孔的钻削方法1261
1.3 钻削加工切削用量的选择1263
1.3.1 钻头磨钝标准1263
1.3.2 钻头的耐用度1263
1.3.3 高速钢钻头钻削不同材料的切削用量1264
1.3.4 硬质合金钻头钻削不同材料的切削用量1265
1.3.5 群钻加工钢件时的切削用量1266
1.3.6 群钻加工铸铁时的切削用量1266
1.4 麻花钻钻孔中常见问题产生原因和解决方法1267
2 扩孔1269
2.1 扩孔方法1269
2.2 扩孔钻的切削用量1269
2.3 扩孔钻扩孔中常见问题产生原因和解决方法1270
3 锪孔1271
3.1 锪钻1271
3.2 高速钢及硬质合金锪钻加工的切削用量1272
3.3 锪孔中常见问题产生原因和解决方法1272
4 深孔钻削1272
4.1 深孔钻削的适用范围、加工精度与表面粗糙度1272
4.2 深孔加工中每次进给深度1273
4.3 内排屑深孔钻钻孔中常见问题产生原因和解决方法1273
5 铰削1274
5.1 铰削方法1274
5.1.1 铰刀直径的确定及铰刀的研磨1274
5.1.2 铰刀在使用中的修磨1275
5.1.3 铰削余量的选择1275
5.1.4 铰削时切削液的选用1276
5.1.5 手工铰孔应注意的事项1276
5.1.6 机动铰孔应注意的事项1276
5.1.7 圆锥孔的铰削1276
5.2 铰削加工切削用量的选择1277
5.2.1 铰刀磨钝标准及耐用度1277
5.2.2 铰削用量1277
5.3 多刃铰刀铰孔中常见问题产生原因和解决方法1279
第9节 镗削加工1281
1 镗刀1281
1.1 单刃镗刀1281
1.1.1 单刃镗刀的装夹方式及用途1281
1.1.2 单刃镗刀的结构形式及主要尺寸1281
1.2 整体式双刃镗刀块1283
1.2.1 双刃镗刀块的形式和应用范围1283
1.2.2 整体式镗刀块尺寸1284
1.3 微调镗刀1285
1.3.1 微调镗刀的结构形式与安装1285
1.3.2 微调镗刀规格系列1285
1.4 组合镗刀头1286
1.5 复合镗刀的形式及应用1287
1.6 镗床用攻螺纹夹头1289
2 卧式镗床镗削1289
2.1 卧式镗床基本工作范围1289
2.2 卧式镗床基本定位方法1290
2.2.1 主轴轴线与镗孔轴线重合方法1290
2.2.2 主轴轴线与后立柱刀杆支架轴线重合方法1290
2.3 导向装置布置的形式与特点1293
2.4 工件定位基准及定位方法1294
2.5 镗削基本类型及加工精度分析1295
2.5.1 悬伸镗削基本方式及加工精度分析1295
2.5.2 支承镗削基本方式及加工精度分析1295
2.6 基本镗削方法1298
2.6.1 用镗模加工方法1298
2.6.2 调头镗削方法1298
2.6.3 垂直孔镗削方法1298
2.6.4 圆柱孔端面刮削方法1299
2.6.5 圆柱孔端面铣削方法1300
2.6.6 镗削内、外沟槽的方法1302
2.6.7 外圆柱面的镗削方法1304
2.6.8 镗孔坐标尺寸的计算1304
2.7 卧式镗床常用测量方法及精度1306
2.8 卧式镗床的镗削用量与加工精度1307
2.9 影响镗削加工质量的因素与解决方法1308
2.9.1 卧式镗床加工中常见的质量问题与解决方法1308
2.9.2 影响孔距加工精度的因素与解决方法1309
3 坐标镗床镗削1310
3.1 坐标换算和加工调整1310
3.2 找正工具与找正方法1310
3.3 坐标测量1310
3.4 坐标镗床的镗削用量与加工精度1315
第10节 刨削、插削加工1315
1 刨削1315
1.1 刨削加工方法1315
1.1.1 牛头刨床常见加工方法1315
1.1.2 龙门刨床常见加工方法1315
1.2 刨削常用装夹方法1315
1.3 刨刀1315
1.3.1 刨刀的结构形式1315
1.3.2 常用刨刀的种类及用途1315
1.3.3 刨刀切削角度的选择1320
1.4 典型零件的刨削1321
1.4.1 槽类工件的刨削与切断1321
1.4.2 镶条的刨削1323
1.5 精刨1323
1.5.1 精刨的类型及特点1323
1.5.2 精刨刀常用的研磨方法1325
1.6 常用刨削用量1325
1.7 刨削常见问题产生原因及解决方法1326
1.7.1 刨平面常见问题产生原因及解决方法1326
1.7.2 刨垂直面和阶台常见问题产生原因及解决方法1327
1.7.3 切断、刨直槽及T形槽常见问题产生原因及解决方法1328
1.7.4 刨斜面、V形槽及镶条常见问题产生原因及解决方法1328
1.7.5 精刨表面常见问题产生原因及解决方法1329
2 插削1329
2.1 常用插削方式和加工方法1329
2.2 插刀1329
2.2.1 常用插刀类型及用途1329
2.2.2 插刀主要几何角度1329
2.3 插平面及插槽的进给量1334
2.4 插削常见缺陷产生原因及解决方法1334
第11节 拉削加工1335
1 拉削方式、加工特点及应用1335
2 拉削装置1339
3 拉削工艺参数1341
3.1 拉刀几何角度的选择1341
3.2 拉削余量的选择1341
3.3 拉削用量1342
3.4 拉削用切削液1342
4 拉削中常见缺陷产生原因与解决方法1344
第12章 难加工材料的切削加工1347
1 常用的难切削材料及应用1347
2 难切削金属材料的可加工性比较1347
3 高锰钢的切削加工1348
3.1 常用切削高锰钢的刀具材料1348
3.2 切削高锰钢车刀与铣刀的主要角度1348
3.3 常用硬质合金刀具车削、铣削高锰钢的切削用量1349
4 高强度钢的切削加工1349
4.1 常用切削高强度钢用高速钢刀具材料1349
4.2 常用切削高强度钢用硬质合金1349
4.3 切削高强度钢的车刀与铣刀的主要角度1349
4.4 车削高强度钢的切削用量1349
4.5 按工件硬度选择铣削用量1350
5 高温合金的切削加工1350
5.1 常用切削高温合金的刀具材料1350
5.2 车削高温合金常用刀具的前角与后角1350
5.3 车削高温合金切削用量举例1351
5.4 铣削高温合金切削用量举例1352
6 钛合金的切削加工1353
6.1 常用切削钛合金的刀具材料1353
6.2 切削钛合金的车刀与铣刀的主要角度1353
6.3 车削钛合金切削用量1354
6.4 铣削钛合金切削用量1354
7 不锈钢的切削加工1355
7.1 常用切削不锈钢的刀具材料1355
7.2 切削不锈钢的车刀与铣刀的主要角度1355
7.3 车削不锈钢的切削用量1355
7.4 高速钢铣刀铣削不锈钢的切削用量1356
第13章 钳工加工及装配1357
第1节 钳工加工1357
1 划线1357
1.1 常用划线工具名称及用途1357
1.2 划线常用的基本方法1361
1.3 划线基准的选择1364
1.3.1 划线基准选择原则1364
1.3.2 常用划线基准类型1364
1.4 典型零件划线举例1364
1.4.1 立体划线1364
1.4.2 典型钣金展开图1366
1.4.3 标准齿轮齿形画法1370
2 锯削1371
2.1 锯削工具1371
2.1.1 锯架1371
2.1.2 锯条1372
2.2 锯削方法1373
3 錾削1375
3.1 錾子的种类及用途1375
3.2 錾子切削部分的几何角度1376
3.3 錾削方法1376
3.3.1 錾板料的方法1376
3.3.2 錾削平面的方法1377
3.3.3 錾削油槽的方法1377
4 锉削1377
4.1 锉刀的分类及基本参数1377
4.1.1 锉刀的各部名称1377
4.1.2 锉刀编号规则1378
4.1.3 锉刀的类别和形式代号1378
4.1.4 其他代号1379
4.1.5 锉纹参数1379
4.2 常用锉刀形式及尺寸1379
4.2.1 钳工锉1379
4.2.2 整形锉1383
4.2.3 异形锉1388
4.3 锉刀的选用1390
4.3.1 锉刀形状的选用1390
4.3.2 锉刀锉纹粗细的选用1390
4.4 确定锉削顺序的一般原则1390
5 刮削1390
5.1 刮削工具1391
5.1.1 通用刮削工具1391
5.1.2 刮刀1393
5.1.3 刮削用显示剂的种类及应用1395
5.2 刮削余量1396
5.3 刮削精度要求1396
5.4 刮削面缺陷的分析1396
6 矫正和弯形1397
6.1 矫正1397
6.2 弯形1397
6.2.1 弯形件展开长度计算方法1403
6.2.2 弯形方法1405
第2节 装配与调整1414
1 装配工艺方法的选择1414
1.1 装配工艺配合方法1414
1.2 各种装配的组织形式1414
1.3 装配工艺规程制订的基本原则1414
2 清洗1415
2.1 常用清洗方法1415
2.2 清洗液的选用1415
2.2.1 水剂金属清洗液配方、工艺参数和适用范围1415
2.2.2 碱液清洗液配方、工艺参数和适用范围1418
2.2.3 混合溶剂配方、主要参数和适用范围1418
3 平衡1418
3.1 转子分类和平衡方法1418
3.2 不平衡量校正方法1418
3.3 静平衡方法及平衡装置1418
3.4 动平衡机类型及用途1421
4 校准1422
4.1 常见校准方法1422
4.2 校准实例1423
5 螺纹连接1424
5.1 螺钉(螺栓)连接的几种形式1424
5.2 螺纹连接的装配要求1424
5.3 有规定预紧力螺纹连接装配方法1425
5.4 螺纹连接的防松方法1426
6 键连接1428
6.1 松键连接装配1428
6.2 紧键连接装配1429
6.3 花键连接装配1429
7 销连接1429
8 过盈连接1430
8.1 压入法1430
8.2 温差法1430
8.3 圆锥面过盈连接装配方法1431
9 铆接1433
9.1 铆接形式1433
9.2 铆接工具1434
9.3 铆钉1434
9.4 铆钉孔直径和铆钉长度的确定1435
9.5 铆接方法1436
9.5.1 铆接加工时应注意的事项1436
9.5.2 铆接方法举例1436
9.6 单面铆接1437
9.7 铆接常见缺陷产生原因及防止措施1437
10 滑动轴承的装配1439
10.1 滑动轴承的分类1439
10.1.1 按滑动轴承润滑的形式分1439
10.1.2 按滑动轴承的结构分1439
10.2 滑动轴承的装配1439
10.2.1 整体式滑动轴承(又称轴套)的装配1439
10.2.2 剖分式滑动轴承的装配1440
11 滚动轴承的装配1441
11.1 滚动轴承的预紧和调整1441
11.2 般滚动轴承的装配1445
第3节 修配技术1446
1 一般零件的拆卸方法1446
1.1 键连接的拆卸方法1446
1.2 销的拆卸方法1446
1.3 滚动轴承的拆卸方法1447
1.4 衬套的拆卸方法1448
2 粘接工艺技术1449
2.1 常用粘接剂的牌号(或名称)固化条件及用途1449
2.2 粘接工艺1452
3 电喷涂工艺1456
3.1 电喷涂修复方法的优缺点1456
3.2 电喷涂修复工艺1456
4 电刷镀工艺1457
4.1 刷镀的一般工艺过程1457
4.2 灰铸铁件刷镀工艺1457
4.3 球墨铸铁件刷镀1457
5 浇铸巴氏合金及补焊巴氏合金工艺1458
5.1 浇铸巴氏合金1458
5.2 补焊巴氏合金1459
第14章 常用技术资料1460
第1节 常用资料1460
1 国家及行业标准代号1460
2 材料线胀系数1461
3 常用材料的密度1462
4 常用材料的滑动摩擦因数1462
5 常用金属材料的熔点1463
6 主要元素的化学符号、相对原子质量和密度1464
7 黑色金属硬度及强度换算1464
8 法定计量单位及其换算1470
8.1 国际单位制1470
8.2 常用法定计量单位与非法定计量单位的换算1471
8.3 常用单位换算1474
第2节 极限与配合、形状和位置公差、表面粗糙度1477
1 极限与配合1477
1.1 术语和定义1477
1.2 基本规定1479
1.3 孔、轴的极限偏差与配合1486
1.3.1 孔的常用和优先公差带(尺寸≤500mm)1486
1.3.2 轴的常用和优先公差带(尺寸≤500mm)1487
1.3.3 孔、轴的极限偏差数值1487
1.3.4 基孔制与基轴制优先、常用配合1501
1.4 未注公差的线性和角度尺寸公差1509
2 形状和位置公差1510
2.1 形状和位置公差符号1510
2.2 形位公差的标注1511
2.3 图样上注出